The difference and connection between hot chamber die casting and cold chamber die casting
Cold chamber die casting and hot chamber die casting are variations of high pressure die casting process. Therefore, the hot chamber casting and cold chamber casting processes are very similar. However, their scope of application is different. This article briefly discusses the differences between these two processes in detail.
Temperature range of hot chamber die casting and cold chamber die casting
Hot chamber equipment for processing low-temperature non-ferrous alloys. The maximum temperature of alloys that can be safely die-cast in a hot chamber machine is around 450°C, including alloys such as zinc, magnesium and lead. In contrast, cold chamber equipment deals with high temperature non-ferrous alloys. It usually handles metal alloys with temperatures of 600°C or above, including alloys such as aluminum, copper, and brass.
The position of the furnace
The alloy melting furnaces are located in different locations and are used for both processes. The hot chamber device has a built-in furnace to melt the metal. Therefore, the metal is delivered directly through the gooseneck to the mold cavity. In the cold chamber die-casting plant, the melting furnace is located externally. The molten metal must be delivered to the machine using either automatic or manually operated ladles.
Production time
Hot chamber machines provide significantly higher casting cycles than cold chamber machines. Although both devices work very similarly, cold chamber casting has a longer cycle due to manual handling of melted metal.
Die life
The hot and cold room machines are built of the same materials. Low melting point alloy is used in hot chamber casting, which has little influence on the die. So, it lasts longer. In contrast, die conditions for cold chamber machines degrade faster because the molten metal has a higher temperature. The die casting alloy is melted in the furnace located inside the equipment, and the die casting alloy is melted in a separate furnace located outside the equipment. The melting and casting cycle of the die casting alloy is significantly shortened, so it has a higher production capacity. Therefore, the production capacity is smaller, suitable for high melting point alloys, has a shorter tool life and requires least safety measures requiring more safety measures. Commonly used metal alloys are zinc, lead and so on. Commonly used metal alloys are aluminum, copper, brass, magnesium and so on.
Longhua provides exclusive hot and cold chamber die casting services
Bengbu Longhua Die Casting Machine Co., LTD is a die casting manufacturing company with strong core competitiveness in China. We have independent intellectual property rights, complete production workshop and experienced technical personnel, equipped with advanced hot and cold room equipment. Below we provide an overview of our hot chamber die casting services and cold chamber die casting services.
Cold room die casting service
Our strong point is our cold chamber die casting machine production capacity. We are experts in aluminum die casting. We can produce machines of all specifications. The capacity of the equipment ranges from 140T to 2000T, and we have the ability to handle any small to large volume die casting projects. In addition, we have internal cleaning and die casting surface treatment facilities. At present, Longhua has cooperated with Hefei Institute of Chinese Academy of Sciences in the upgrading of die casting machines and automation equipment, and has applied the advanced technology of Chinese Academy of Sciences to our equipment production. Therefore, you can get one-stop cold room die casting solutions from us.
Hot chamber die casting service
The tonnage of our hot chamber die casting equipment ranges from 60 tons to 250 tons. As a result, we can handle a variety of die casting projects. Zinc die casting mainly adopts hot chamber equipment.
Hot and cold chamber casting, which is better?
Hot chamber die casting and cold chamber die casting are good methods to produce metal parts. However, the hot chamber process has some advantages over the cold chamber process. It is faster, more economical and safer than the cold chamber process, and provides longer tool life. These characteristics easily lead one to believe that hot chamber casting is better than cold chamber casting. However, their scope of application is different. Therefore, it is difficult to rule out the relative advantages of one approach being better than the other. Hot and cold chamber casting deals with completely different kinds of alloys. For example, you can only die-cast aluminum in a cold room environment. Simply put, when you're dealing with alloys with high melting points, you don't have much choice.
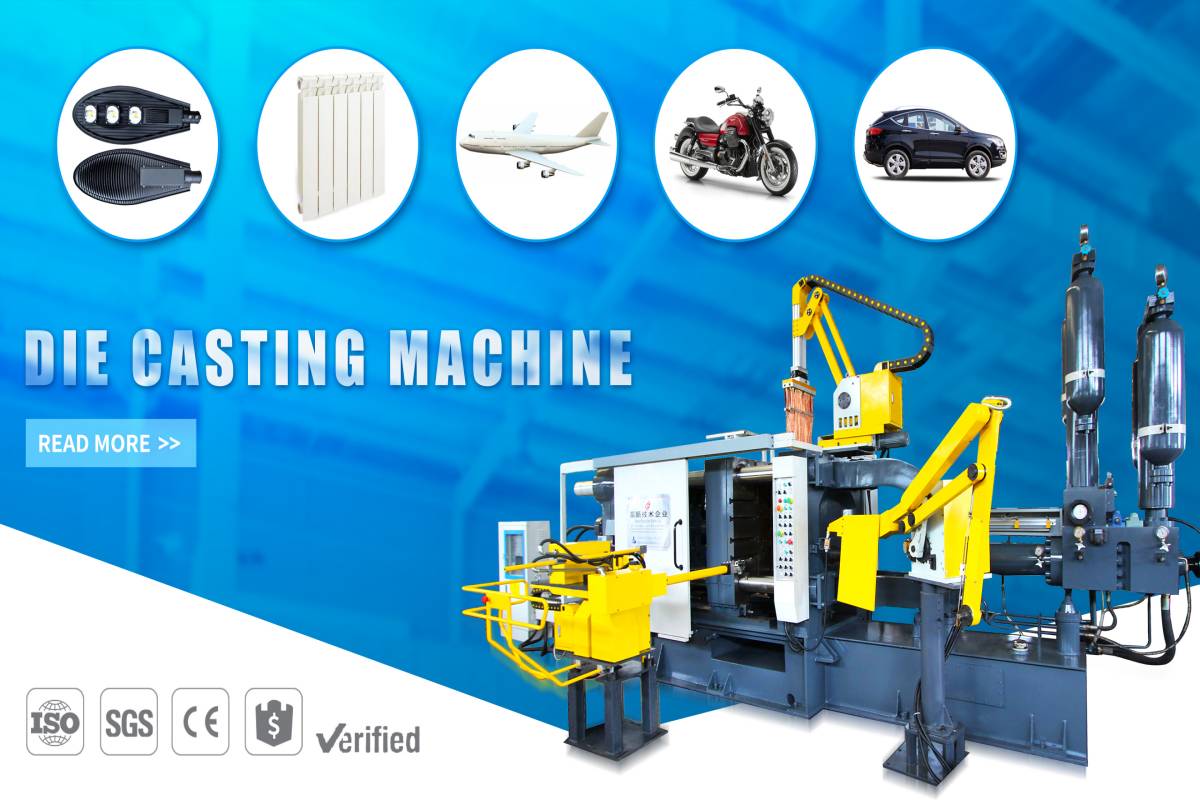